Durable High Pressure Wire Winding Hose
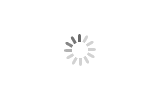
Structurally, the multi-layer wire winding process gives the high pressure wire winding hose super strong pressure resistance, which can withstand hundreds of MPa extreme pressure, far exceeding ordinary hoses. It has excellent performance, good flexibility, adapts to complex pipeline layout, and is easy to install and maintain; it has strong pulse bearing capacity and can operate stably under frequent pressure fluctuations.
Durable Wire Spiral Hose represents a revolutionary advancement in industrial fluid transfer technology, with its multilayer structure delivering exceptional performance under extreme operating conditions. The core of High Pressure Wire Spiral Hose lies in its precision-engineered steel wire reinforcement layer, where high-tensile steel wires are wound in a tightly interlocked spiral pattern using computer-controlled winding technology. This armored construction forms a three-dimensional stress dispersion network that enables the hose to withstand sustained pressures up to 420 MPa while maintaining flexibility - a 300% improvement over conventional rubber hoses. The durable polyurethane inner lining, reinforced with abrasion-resistant additives, ensures chemical compatibility with over 200 industrial fluids including hydraulic oils, acid-base solutions, and high-temperature steam.
As the ultimate solution for heavy-duty applications, Durable Wire Spiral Hose demonstrates remarkable environmental adaptability. Its zinc-aluminum alloy coated steel wire layer provides corrosion resistance exceeding ISO 9227 salt spray test standards, while the specially formulated outer cover resists ozone degradation and maintains flexibility at temperatures ranging from -54°C to +150°C. These technical advantages make High Pressure Wire Spiral Hose indispensable across multiple industries. In petrochemical operations, it safely transports supercritical CO2 and catalytic reagents at 35MPa working pressures. The construction sector relies on its 8000+ bend cycle durability for concrete pump systems, while mining applications benefit from its rock abrasion resistance certified by MSHA standards.
The manufacturing process of Durable Wire Spiral Hose incorporates aerospace-grade quality control measures. Each production batch undergoes rigorous testing including 250% proof pressure verification, impulse testing exceeding 200,000 cycles at 1.5×WP, and vacuum integrity checks. These stringent controls ensure the High Pressure Wire Spiral Hose meets API 17K, EN 853, and SAE J517 simultaneously - a rare triple certification in hose manufacturing. Recent innovations include the integration of smart monitoring layers with embedded pressure sensors, enabling real-time condition monitoring through IoT connectivity.
Marine engineers particularly value the High Pressure Wire Spiral Hose for its seawater corrosion resistance and anti-kinking properties in confined engine rooms. A single 1" ID hose can replace traditional brass piping systems while reducing weight by 60% and installation time by 45%. The Durable Wire Spiral Hose's vibration damping characteristics also prove critical in offshore drilling platforms, where it maintains seal integrity under 7.0 magnitude equivalent vibrations.
Maintenance protocols for High Pressure Wire Spiral Hose emphasize its lifecycle advantages - proper installation extends service life to 8-10 years even in continuous operation, with annual inspection intervals recommended. The hose's non-conductive outer layer meets ATEX directives for explosive environments, while its smooth bore design maintains turbulent flow efficiency above 98%. As industries increasingly adopt automation, the Durable Wire Spiral Hose continues to evolve, with next-generation models featuring graphene-enhanced composites for 600MPa pressure capacity and self-healing nano-coatings - cementing its position as the gold standard in high-pressure fluid transfer solutions.