Intercooler Turbocharger Rubber Air Pipe
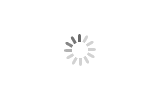
Excellent flexibility: With good flexibility, it can flexibly adapt to the vibration and displacement generated when the engine is working, ensuring stable and reliable air delivery under various complex working conditions and maintaining stable operation of the system.
Performance improvement assistance: It helps improve the engine intake efficiency, optimizes the combustion process, and thus enhances the engine power output, while reducing fuel consumption, comprehensively improving the performance of the vehicle, and providing strong support for the efficient operation of the vehicle.
Turbocharger Air Pipe & Intercooler Air Hose System: Advanced Thermal Management with EODM Rubber Tube Technology
As the critical link between forced induction components, the Turbocharger Air Pipe and Intercooler Air Hose form an optimized airflow network for modern turbocharged engines. Engineered around breakthrough EODM Rubber Tube (Ethylene Octene Diene Monomer) technology, this system balances extreme temperature resilience with precision airflow control across automotive, marine, and industrial applications.
1. Core Functional Synergy
The Turbocharger Air Pipe channels 200°C+ compressed air (30-40 psi) from the turbo outlet to the intercooler, while the Intercooler Air Hose delivers cooled air (-20°C post-intercooler) to the intake manifold. This thermal management cycle increases air density by 35-50%, directly translating to combustion efficiency gains and 15-20% NOx reduction in Euro 7/Tier 5 engines.
2. EODM Rubber Tube Material Superiority
The Intercooler Air Hose leverages EODM Rubber Tube’s unique molecular structure to outperform conventional materials:
Temperature Range: Maintains flexibility from -50°C (arctic cold starts) to 220°C (turbo overshoot conditions)
Pressure Stability: Withstands 45 psi pulsations via dual-layer nylon cord reinforcement
Chemical Resistance: 90% less swelling vs. standard EPDM when exposed to direct oil blow-by
Vibration Absorption: Reduces turbo-induced harmonics by 60% through tuned elastomer damping
3. System-Specific Engineering
Intercooler Air Hose Breakthroughs:
Multi-layer EODM Rubber Tube construction:
Aramid fiber reinforcement for 4:1 burst pressure safety margin
4. Performance Validation
Both Turbocharger Air Pipe and Intercooler Air Hose undergo 35+ industry tests:
Thermal Shock: 500 cycles between -50°C and 250°C (IATF 16949 compliant)
Pressure Fatigue: 1 million pulsations at 2× operational PSI
Chemical Immersion: 1,000hrs exposure to bio-diesel/AdBlue mixtures
Abrasion Resistance: 50,000+ Taber cycles simulating underhood wear
5. Application-Specific Configurations
High-Performance Vehicles:
Turbocharger Air Pipe with ceramic-coated surfaces reduces heat rejection by 40%
Intercooler Air Hose featuring 120mm ID EODM Rubber Tube supports 800hp+ builds
Commercial Trucks:
Steel-braided EODM Rubber Tube hoses withstand 500kPa boost pressures
Corrosion-resistant aluminum couplings for maritime environments
Hybrid Platforms:
Electromagnetically shielded Turbocharger Air Pipe prevents EMI interference
Flame-retardant EODM Rubber Tube formulations meet EV battery compartment standards
6. Maintenance & Sustainability
Predictive monitoring via IoT-enabled pressure/temperature sensors embedded in Intercooler Air Hose walls
150,000-mile service intervals with 85% recyclable EODM Rubber Tube materials
Closed-loop manufacturing recovers 92% of production waste
7. Future-Ready Innovations
Phase-change EODM Rubber Tube compounds that actively cool intake air
Self-sealing Turbocharger Air Pipe designs healing ≤3mm punctures autonomously
AI-optimized hose geometries reducing pressure drop by 25%
This Turbocharger Air Pipe and Intercooler Air Hose system with EODM Rubber Tube technology delivers uncompromised thermal management – proven to reduce intake air temperatures by 28°C versus legacy systems while withstanding 10,000+ thermal shock cycles without performance degradation.